Ein Schlüssel zum Erfolg
Das 2016 im nordböhmischen Ostrov neu eröffnete WITTE-Werk ist im Fertigungsverbund mit dem 20 km entfernten Werk Nejdek auf die Herstellung von Türgriff-Einheiten samt den damit verbundenen Technik-Modulen spezialisiert. In Ostrov wird insbesondere Kunststoff-Spritzguss, Lackierung und Montage betrieben. Eine wesentliche Anlagenkomponente ist die hochautomatisierte zentrale Förderanlage für Kunststoffgranulat zu den Spritzgießmaschinen. Sie wurde von der deutschen motan-Gruppe geliefert und von deren österreichischer Handelsvertretung Luger GmbH geplant und montiert.
Die Formen-, Farben- und Funktionsvielfalt der bei WITTE Automotive in Ostrov gefertigten Türaußengriffe und Verriegelungseinheiten ist beeindruckend. Sie entsprechen den gültigen Crash-Sicherheits-Bestimmungen, sind mit und ohne Fernbetätigung bis hin zur schlüssellosen „Passive Entry/Passive Go“-Bedienung ausgeführt und auftragsbezogen auf die spezifizierte Wagenfarbe abgestimmt. Abgerundet wird das Angebot durch die patentierten „Anti-picking“-Maßnahmen zum Diebstahlschutz.Insgesamt geht das Angebot von WITTE Automotive weit über die Außengriffe hinaus und enthält auch die Schließbügel, Tür-Innenbetätigungen, Schlüssel und Schlösser, wo noch benötigt Zuziehhilfen, Türfeststeller und Türbremsen, Türantriebe bis hin zu Tür-Protect-Systemen.
Ähnlich umfangreich ist das Lieferprogramm für Front- und Heckklappen. Dabei kommen neben elektromechanischen Schlössern auch elektrische Schließbügel für angetriebene Heckklappen oder montagefreundliche Griffleisten zum Einsatz. Insbesondere die für Fronthauben entwickelten Lösungen verbinden anspruchsvolle Aushebekurven mit kompakter und stabiler Bauweise. Sie sind beispielsweise Teil des Konzeptes der „aktiven“ Motorhaube zur Erhöhung des Fußgängerschutzes, die im Kollisionsfall durch pyrotechnische Auslösung angehoben wird und so die Frontknautschzone weicher macht.
Auch für PKW-Sitze steht ein umfangreiches Produktspektrum zur Verfügung. „Energie absorbierende Lehnenschlösser und Schließbügel minimieren in Crashsituationen die Rückenlehnenbelastung. Sie sind Teil der Sicherheitsausrüstung zum Insassenschutz. Neuartige Sitzbodenverriegelungen für das komfortable Entnehmen und Einsetzen von Sitzen sowie das aktive Sicherheits-Rückenlehnensystem (ASR) runden das WITTE-Programm ab“, wie David Svoboda, Bereichsleiter Spritzguss, in seiner Unternehmensvorstellung zusammenfasst.
Kompromisslose Kunststoffteile-Qualität
Die Griffmodule werden als „Car sets“ gefertigt. Ein Set umfasst alle Türgriffe eines Fahrzeuges samt den dahinter liegenden Funktionen. Die Strukturteile werden aus Festigkeitsgründen aus PA6 mit 35 Prozent Glasfasern gefertigt, die Abdeckungen aus einem PC/ABS-Blend. Eingesetzt wird ausnahmslos voreingefärbtes Material. Produziert wird aktuell auf 12 Spritzgießmaschinen, 10 weitere sind in konkreter Planung.
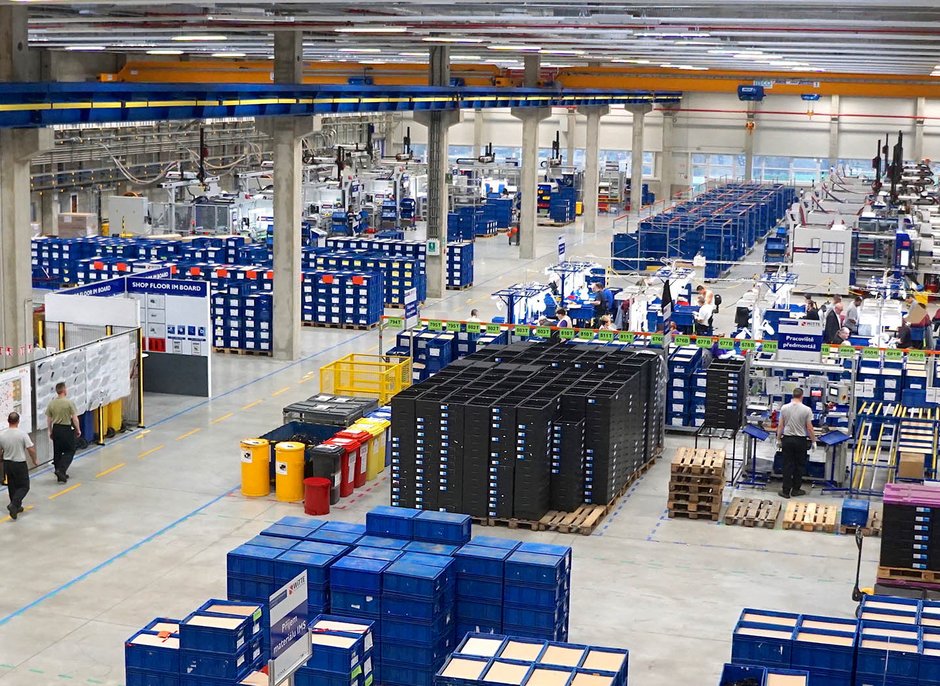
Ein Großteil der Griffe wird durch Nutzung der Gasinjektionstechnik als Hohlkörper gefertigt. Dies bedingt, dass bei jedem Produktionszyklus ein Materialanteil in der Größenordnung von 30 bis 40 Prozent des eingespritzten Kunststoffvolumens in eine Nebenkavität verdrängt wird, die anschließend abgetrennt, gesammelt und nach dem Zerkleinern wieder in den Materialstrom rückgeführt wird. „Zur Unterstützung der Oberflächengüte müssen alle Materialien, sowohl Neuware, als auch das Regenerat bis zu einem Restfeuchtigkeitsgehalt von 0,1 bis 0,15 Prozent (PA6) bzw. 0,02 bis 0,05 Prozent (PC/ABS) getrocknet werden“, erklärt Pavel Karas, Abteilungsleiter Spritzguss im Werk Ostrov, beim Gang durch die Produktion entlang der Materialförderanlage. Deshalb kam für uns nur ein Anlagenlayout in Frage, bei dem alle verarbeiteten Kunststofftypen inklusive der Regeneratmengen über eine zentrale Trocknungsanlage mit Trockenluft zu den Maschinen geführt werden.“
So sehr die Trocknungsanlage das anwendungstechnische „Herz“ des Materialversorgungssystems ist, so einfach konnte die Materialaufgabe an der Spritzgießmaschine gehalten werden. An der Maschine wurde ein Mischgerät vorgesehen, um Neuware mit Regenerat, sowie einem Additiv zu mischen. Unter dem Dosiergerät befindet sich ein Metalldetektor, um allfällig im Mahlgut enthaltene Messerspäne abzutrennen.
Gesamtanlage über Produktionsleitrechner transparent bedienbar
Alle Anlagenkomponenten mit Ausnahme der Dosiergeräte an den Spritzgießmaschinen werden über die von motan dafür spezifisch entwickelten Elektronik-Module angesteuert und bedient. Sie sind über ein Ethernet bzw. TCP/IP zu einem CONTROLnet zur zentralen Anlagensteuerung verbunden. Diese ist mit dem umfassenden Anlagen-Managementsystem LINKnet kombiniert, das die Prozessabläufe und Anwendungsdaten erfasst, protokolliert und über das alle angeschlossenen Steuerungen bis hin zur Geräteebene bedient werden können. Außerdem wurde eine Schnittstelle zum bestehenden ERP (Enterprise-Resource-Planning)-System realisiert.
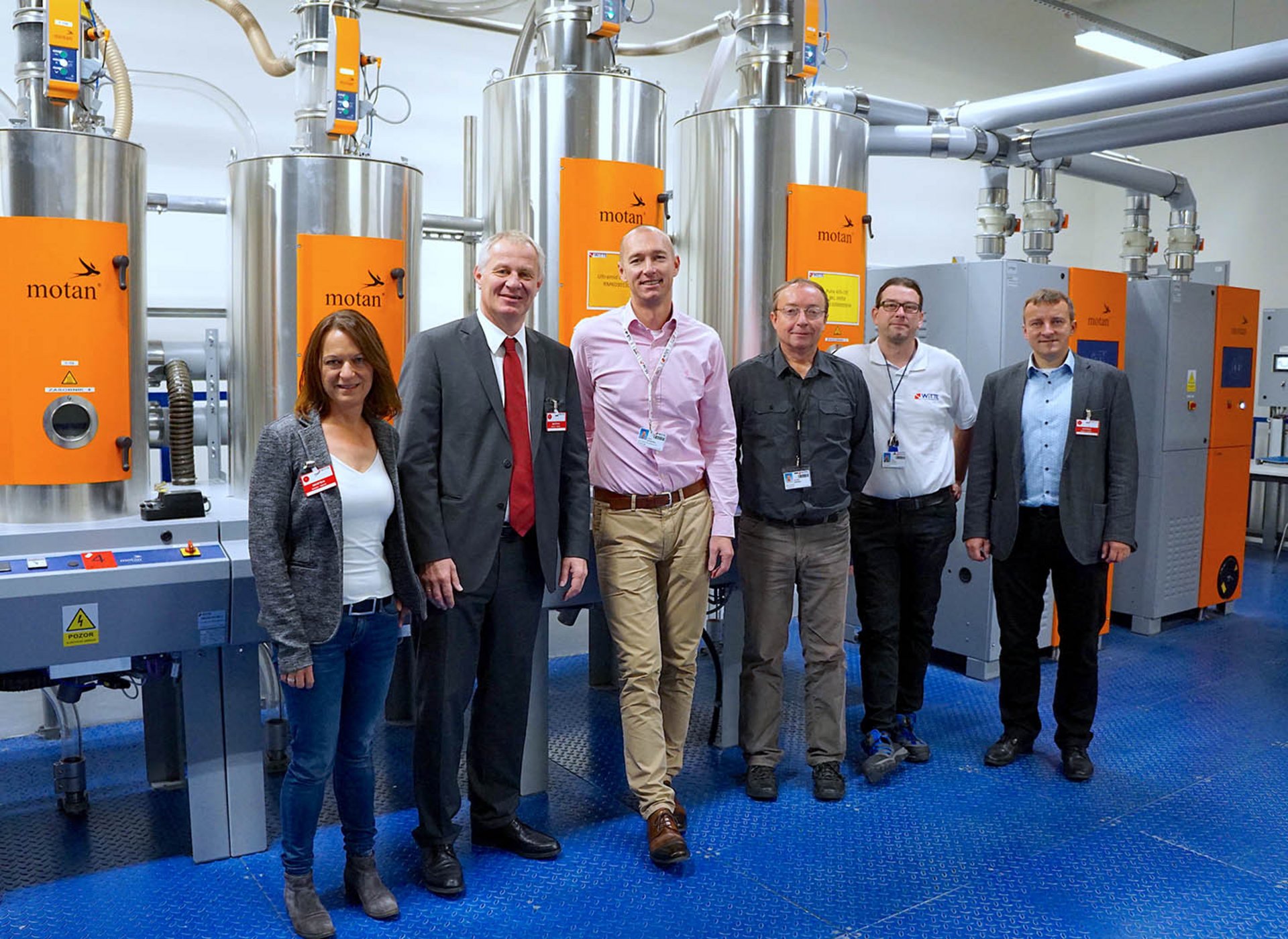
Abschließend fasst Bereichsleiter Svoboda in seinem Resümee zum Produktionsstart das wesentliche Kriterium für die Entscheidung pro motan zusammen: „Angesichts des engen Zeitplans beim Bau und der Inbetriebnahme unseres neuen Produktionswerkes war uns wichtig, das technische Risiko bei möglichst allen Anlagenkomponenten so gering wie möglich zu halten. Nach einer Reihe von beeindruckenden Referenzbesuchen haben wir uns schließlich für motan-colortronic als Systemlieferanten und Luger als Anlagenplaner und Servicepartner entschieden - und wurden nicht enttäuscht.“.