01 - What is meant by “dosing” in the context of injection moulding?
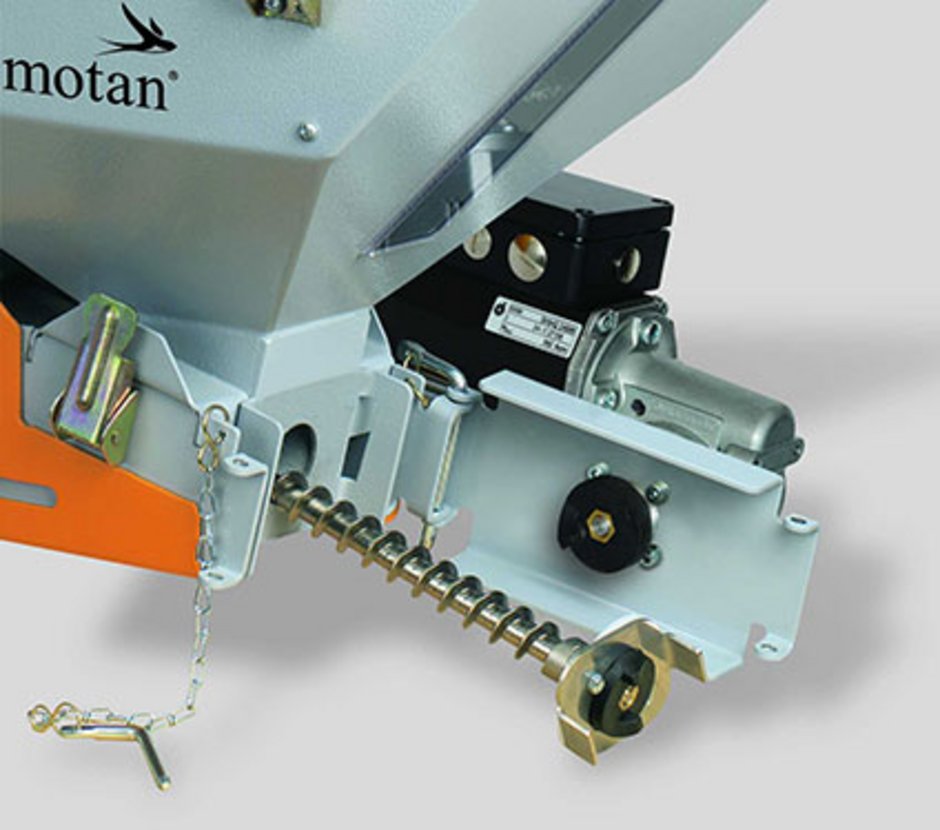
The great benefit of plastic is its versatility and flexibility. By altering ingredients and additives, you can create precisely the right compound for a given application – changing the material’s mechanical properties, resistance to chemicals or its colour.
There is a downside to these possibilities, however. On the one hand, because there is such a vast array of ingredients to choose from, it makes little economic sense for the raw materials industry to individually customise their offerings to the many diverse wishes of plastics processors – especially as the lot sizes they want to buy continue to shrink.
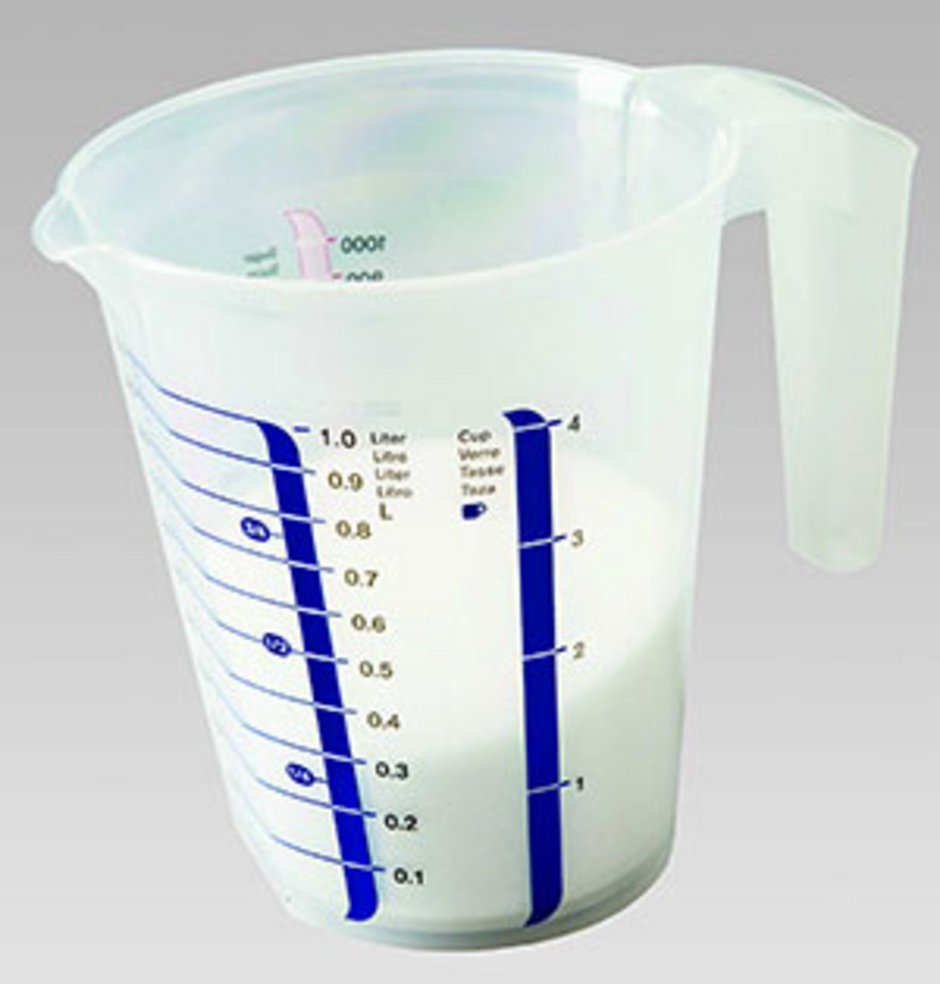
Yet on the other hand, plastics processors are faced with demands from their end customers, who in light of ever-shorter product lifecycles are clamouring for new materials to be made available rapidly. The solution? Plastics processors can either buy readymade compounds or create them themselves.
Readymade compounds are usually not the most cost-effective solution, as a premium is often charged for small lot quantities. Moreover, they leave little wiggle room if you want to change the composition at short notice.
For greater flexibility, it makes sense to mix the material yourself. There are two ways to do this: blend the recipe centrally (manually or automated) or dose and mix directly at the throat of the processing machine (automated). Whichever method you choose, it is imperative that you follow the recipe to the letter: all quantities and ratios must be exactly right.
When mixing the recipe manually, the individual components are weighed by hand before being combined often with a cement mixer. On the face of it, there is nothing wrong with this method. But there are serious drawbacks – in terms of wastage and material segregation issues, for example. It can be difficult to correctly estimate how much of the mix you will ultimately need. And if you get the recipe wrong, you can be left with a significant amount of expensive but useless leftovers.
In contrast, working automatically at the throat of the processing machine offers multiple advantages. It allows you to mix recipes on demand and at short notice, changing the recipe is quick and easy, and results are visibly fast. Surplus material is kept to a minimum, and recipes can be easily reproduced.
Dosing is an essential stage of this process – combining two or more components in precisely the right ratio. Whether the ingredients are granules, powders, paste or liquid, a number of basic principles apply. A dosing device in the dosing and mixing unit draws an exact amount of material from a supply hopper or similar container and transfers it to a reservoir or directly into the throat of the processing machine. Because it is responsible for measuring the ingredients with pinpoint precision, the dosing device plays a crucial role in the final outcome.
The choice of dosing device depends on the type of material and its properties. As solids tend to be the preferred material for injection moulding, the metering device must be able to dose granules, micro-granules or powders.
A number of material properties must be taken into account. Rheology – that is, how the ingredient flows – is particularly important: powder can, for example, be free-flowing, sticky or can fluidise. In addition, granules can be rigid or flexible, and they can be brittle and easily damaged. Regrind has its own dosing issues as it usually lacks a uniform consistency and contains more dust.
Dosing screws are suitable for the vast majority of applications. Other forms of dosing device include cone valves, disc dosing elements, slide-gate valves, dosing chambers and rotary valves. One dosing device that will be familiar to everyone is the measuring cup used for baking. And just as in baking, one rule matters above all else – whatever you are manufacturing, accuracy is everything: components must be measured with 100% precision.
Further important factors include whether the dosing system is volumetric or gravimetric, and how the ingredients are mixed – these points and many more will be explained by Mo in more detail in upcoming columns.
You want to see how automatical dosing can look like? Find more information on www.motan.com