23 - What is important for material flow in plastics processing?
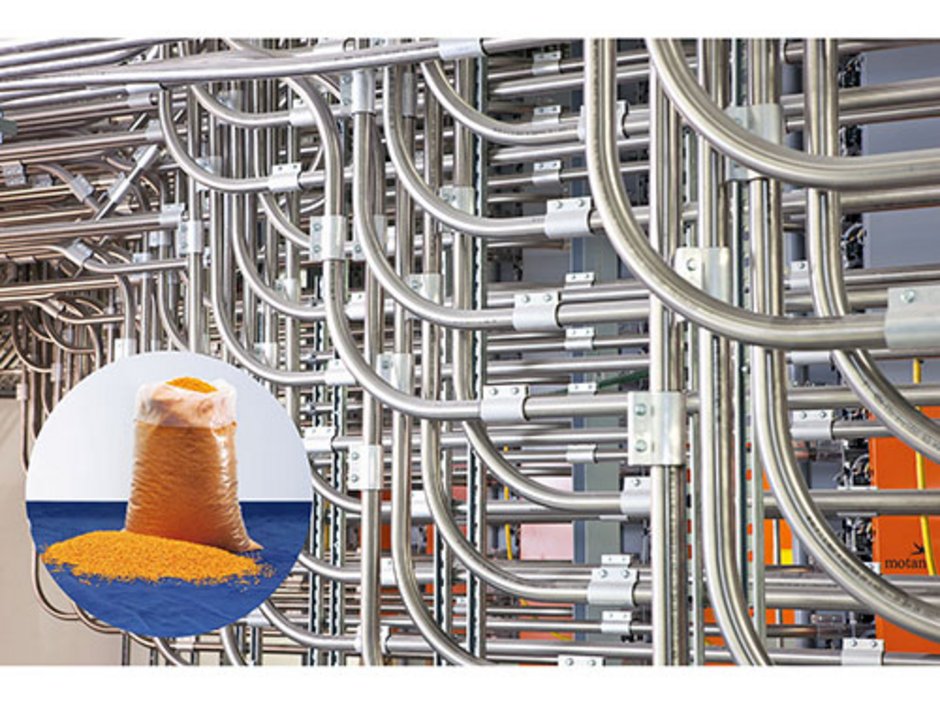
Now that mo’s corner has dealt with the dosing and drying of plastics extensively, this issue will turn to the third chapter of material handling in plastics processing with the topic “conveying”.
To transport material from A to B – to be more precise from storage location to processing machine – may at first seem relatively uncomplicated. This was certainly the case at the start of plastics processing when sacks and buckets were sufficient. But the rise of automation, shorter cycle times, more demanding plastics, today’s partially very high throughputs, and many other factors have made manual supply no longer practical. After all, the goal is an increasingly economic, safe and flexible (small production batches) production.
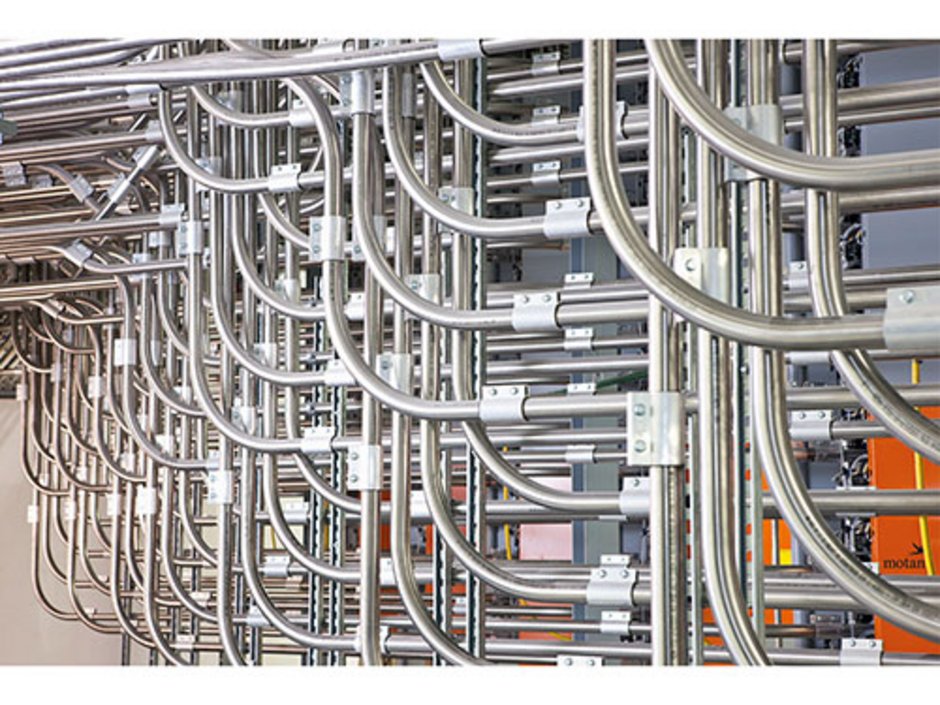
Therefore, plastics processing machines today are predominantly fitted with suction material loaders. While we‘re at it: In this context there is often talk of so-called “separators”, which refer to nothing other than material loaders.
In the simplest cases a stand-alone loader on the unit may suffice. Here it is important to consider that a container with the raw material must be next to the unit. It becomes more complicated when material will be conveyed to the unit from a greater distance, perhaps from a central supply station, from silos, or a drying system.
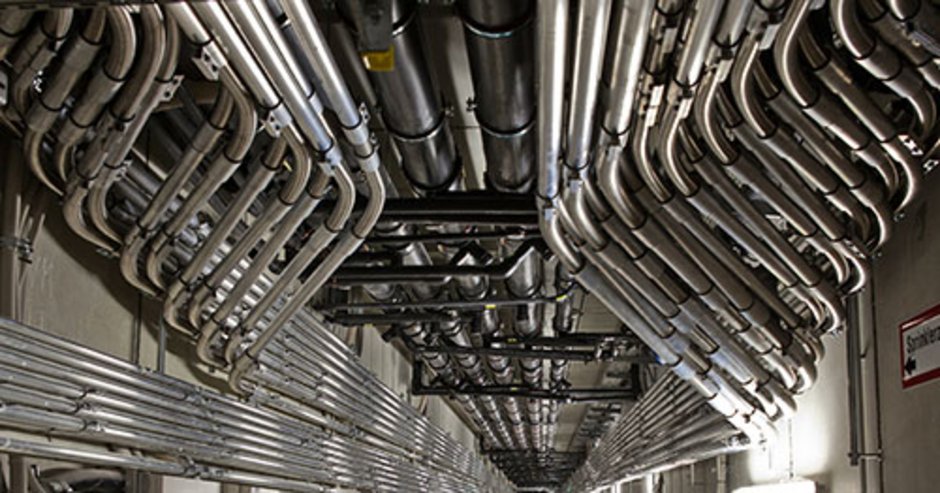
Many questions need to be clarified for the design of a practical, operationally reliable and economic material supply. Some of the terms relevant for the selection of the required and suitable components are: Storage, material charge and material distribution, conveying type, conveying speed, stand-alone conveying or central conveying system, vacuum conveying, production environment (clean room), system controls and plant layout.
In this context, the conveying physics in consideration of the material to be conveyed should not be underestimated, as the material should reach processing as gently as possible. This is illustrated by a quick glance at the variety of plastic types which are available in diverse material types (granulate, pellets, regrind, flakes, fibre or powder), each with specific flow characteristics.
mo’s corner will present the options that are available for raw material supply in plastics processing and the aspects that need to be considered in detail concisely and comprehensibly in the upcoming issues.
You need suitable equipment for your conveying process? Click here for help: www.motan.com