35 - What is important when choosing and installing pipe lines?
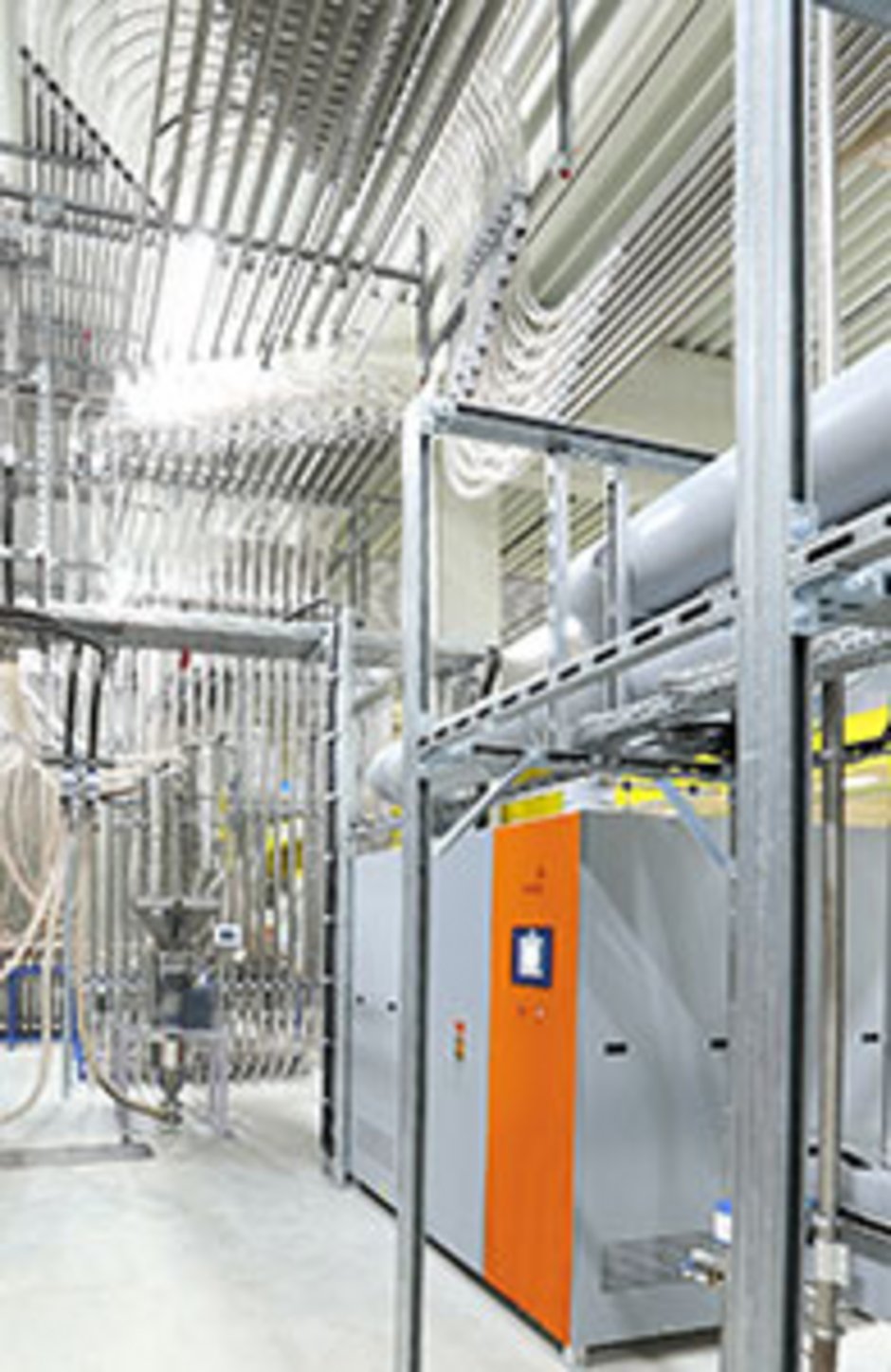
Through pipe lines and hoses from the material source to the processing machine – the distance that material has to cover during material processing can be vast for individual cases.
Depending on the local conditions, conveying distances of hundreds of meters need to be bridged. In a complex setup, kilometres of material and vacuum feed lines may be necessary to supply the machines. Connecting the rigid pipelines with the material loaders usually occurs with flexible, vacuum-proof hose lines with integrated steel coils. Standard diameters for material feed lines in plastics processing are roughly 40 – 70 mm.
Material feed lines are often aluminium due to reasons of costs and weight, but their limited stability can be problematic. Stainless steel pipe lines are more effective, particularly if abrasive material needs to be processed. In special cases, e.g. clean room production, pipes made from borosilicate glass can also be considered. The pipe bends, which are subject to extreme abrasion, are often made from stainless steel or special glass. In order to minimise the impact area of granulate during a direction change, the bends are gently curved with large radii.
Wear and abrasion of conveying material and pipe lines is important in general. Particularly for dilute phase conveying, which is common for granulate, product abrasion can occur mainly due to the high speeds. The surface properties of the pipe’s inner surface play an important role here. Smooth surfaces can contribute to the generation of films and angel hair (thread-like impurities from partly plasticised wear debris), which can lead to the risk of blockages. Rough surfaces, on the other hand, can lead to fine wear debris (dust). The loss of material in this context should not be underestimated, as well as potential problems during processing. Pipe lines with a defined surface structure can be a solution. Finding the optimal compromise between suitable inner surface of the pipe and conveying speed depends on the individual situation and requires a lot of experience. It is also sensible to purge vertical material feed lines after every conveying cycle, in order to prevent material plugs. Material feed lines should also be earthed in order to protect them from static electricity, even though this is not always specifically required.
Many processors wrap their pipe lines in commercially available foam pipe insulation to reduce the noise during material transport. The foam also provides thermal insulation, which is beneficial for pre-dried and heated material. The downside is that damaged caused by abrasion is spotted too late. A more elegant solution would be double-walled pipe systems which reduce the noise levels considerably and stop heat loss like an insulated window. Combined with integrated flow indicators, they can help identify and pin-point leaks.
How can pipe lines connect material source and processing machine in practice? For examples please visit www.motan.com