49 - How can material stress be reduced during conveying?
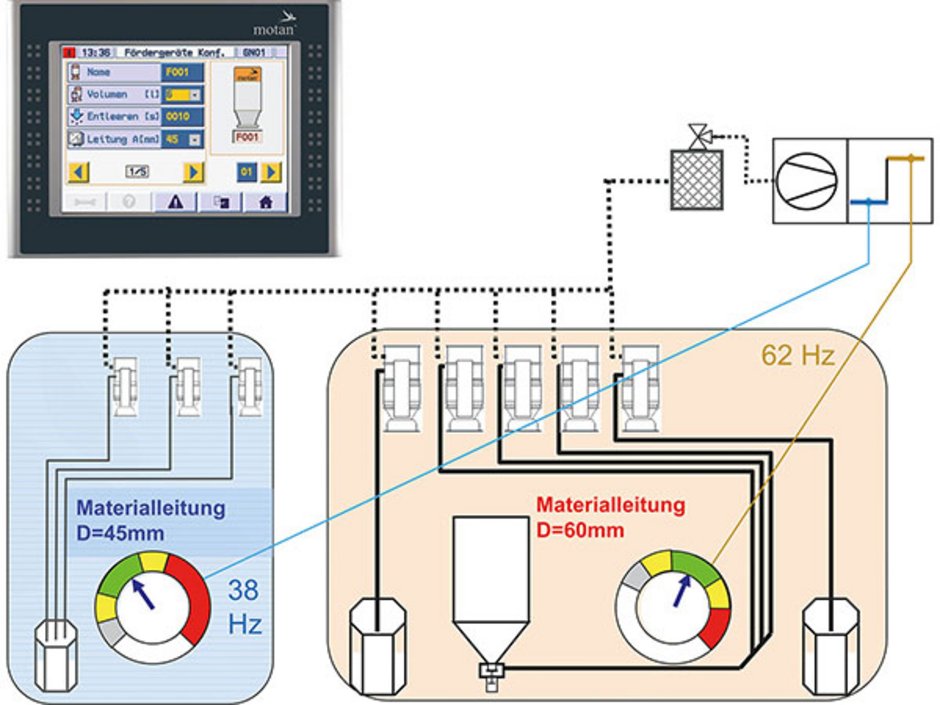
In issues 35 and 37 we described some different forms of abrasion and signs of wear, as well as listed some possible precautions to reduce wear and abrasion. A quick reminder: The cause of abrasion and wear of material, pipe systems and material loaders is often a combination of mechanical and thermal stress. The Conveying speed also plays an important role.
Therefore, the best possible compromise between gentle material conveying and desired throughput performance should be found when designing conveying systems. Crucial factors here are also conveying distance, flow properties of the material, performance of the vacuum generator and diameter of the material feedline. Nominal diameters of approx. 35-70 mm are usual in plastics processing.
Processors are always looking to optimize and increase productivity. This results in increased demands on the conveying systems due to the greater required throughputs (often combined with the use of larger machines) and possibly longer conveying distances. This affects, for example, the selection of a suitable vacuum generator, as its performance must match the maximum requirements. It may also be the case that material feedlines with larger diameters are needed.
In view of the above, it is sensible to equip the material supply with a modern conveying control which will automatically take the individual conditions of the connected material loader into account, such as conveying distance, material to be conveyed, and pipe diameter. A prerequisite for this is a blower which has adjustable throughput performance and a correspondingly intelligent control.
The blower performance can be configurated for every material loader with data for material type, throughput performance, pipe diameter, and conveying distance from material source to destination. As a result, the control can individually generate the required air flow for an optimal conveying speed for each material loader.
Once the control has been set up, the material supply runs completely automatically. However, there is still the possibility of manual precision tuning.
Controls like this have many benefits: saved settings can be recalled at any time, which reduces operating errors. Because the system does not operate permanently in full load operation, the reduced speed prevents abrasion and wear of the material, the pipes, and the material loaders. During planning, the power reserves of the conveying system can be calculated, resulting in increased planning security when expanding the system. Line systems with different (fitted) pipe diameters are cheaper and over or under sizing of the diameters is avoided. And finally, when the blower performance is reduced, it uses less energy.
You want to see conveying equipment in practice? Visit www.motan.com for a huge range.