52 - How can re-moisturisation at high air humidity be prevented?
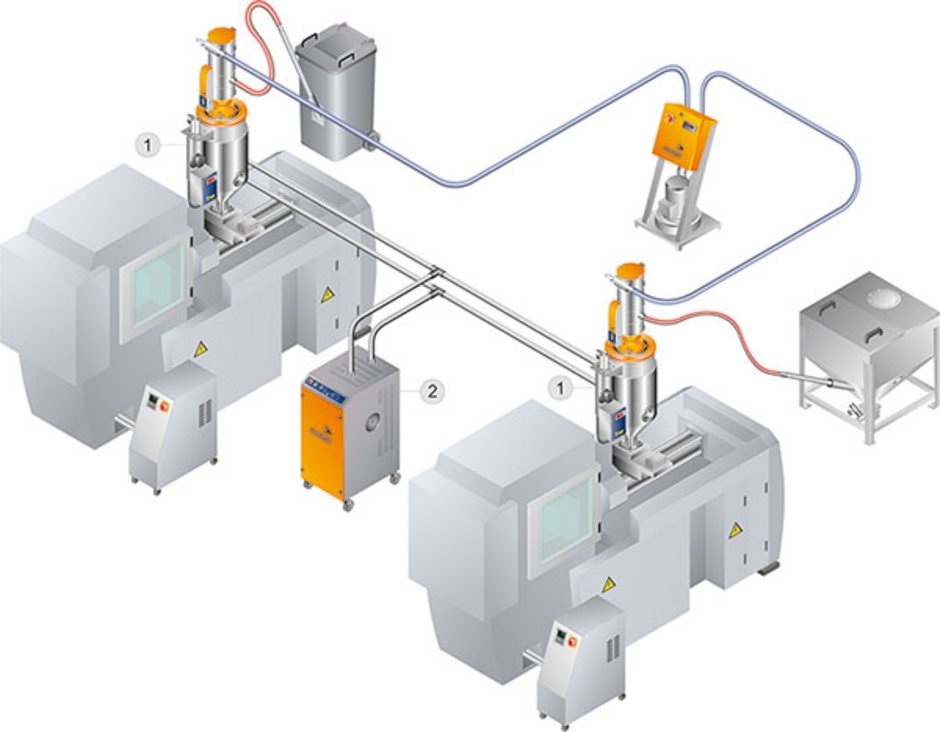
The following basic principle applies: if plastic granulate is stored in environmental air, its moisture content will adjust to match the moisture present in the air until both moisture contents are the same. For hygroscopic plastics this can happen very quickly if air humidity is high, such as in summer. In general, re-moisturisation depends on climatic conditions, the time of year, storage duration & location and the material itself.
The consequences are problematic from both a technical and economical perspective. If the predetermined processing or residual moisture is not correct, this will affect the process safety and product quality. In addition, there are also economic consequences, as the material may need to be dried again or for significantly longer than originally required.
The goal, then, is to retain the dry condition, i.e. to prevent the material reabsorbing moisture between delivery and processing. In this context it is also important to bear in mind that material is often delivered pre-dried.
For silos and octabins a solution is to blanket the material with dry air, and for silos cold air is also suitable in this case. For octabins there is a very simple way of preventing re-moisturisation: once the suction probe is in the material, the internal foil sack can be securely tied to the suction pipe. If this isn’t possible, a cover over the octabin may be useful. However a combination with blanketing would be ideal – depending on the individual case with either dehumidified air or, better, with dry air.
There is the danger of re-moiturisation particularly for hycroscopic materials on route to the processing machine, both during conveying and while in the hopper loader on the processing machine. With the following measures, which can be combined, this can be prevented:
- Conveying with dry air – in this case conveying occurs in a closed cycle with dried air.
- Reduce material supply at the processing machine – this possibility is suited for small throughputs, and material supply at the machine is kept as small as possible. In order to prevent material shortages, the conveying system must be specifically adjusted to this.
- Drying at the machine – if a material is only being processed at one machine, it can be dried at or on the processing machine. For small throughputs a compressed air dryer is often used. An alternative is an offset drying bin that is installed on the machine. The dry air generator is then located next to the machine.
- Final drying or blanketing at the machine – here the actual drying process occurs in a “normal” central drying system. On the respective machine an additional dryer is located that blankets the material with dry air. Usually only smaller compressed air dryers are suited.
In all cases it is important to bear in mind that air from a hot air dryer is normally not suited for blanketing, as these dryers operate with environmental air. In the worst case the material could end up with a higher moisture content than before “drying”. A better alternative is the use of relaxed compressed air.
You want to see different types of dryers? Please click here for more information: www.motan.com