53 - When is a return air cooler necessary?
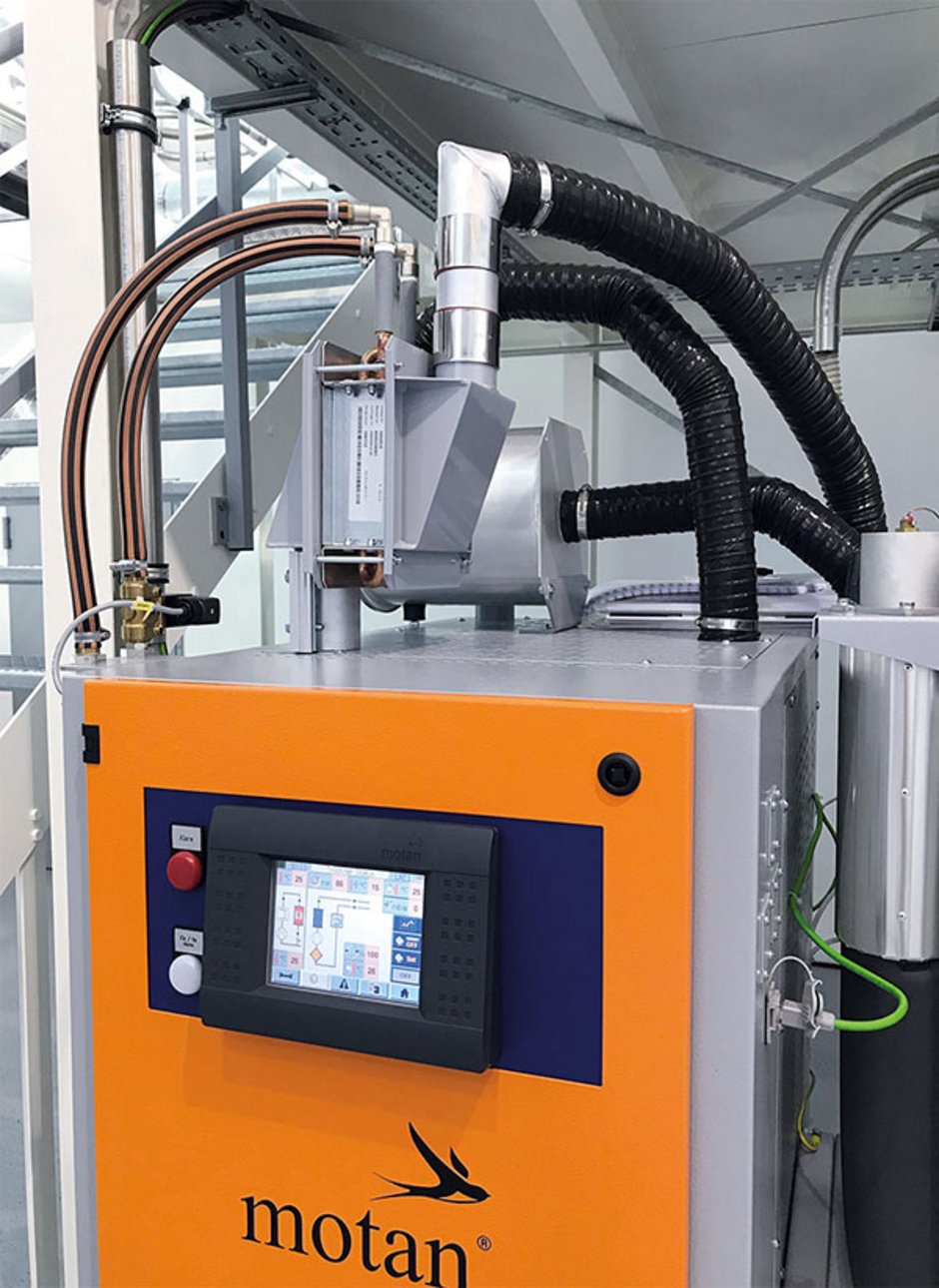
In issues 50 and 51 we looked at how molecular sieves – also called desiccant beds – operate and how they are regenerated.
Specifically at high drying temperatures and/or dry air dryers without automatic air flow regulation the temperature of the return air, and then also the temperature of the active molecular sieve, plays an important role. This is because the desiccant’s water adsorption capacity is reduced at higher temperatures.
Return air refers here to the dry air (process air) after it has flowed through the material in the drying bin, taken on moisture and has then been directed through the molecular sieve.
A quick reminder: When drying plastics, the amount of dry air as well as drying temperature, dew point, and drying time, play an important role. The amount of dry air is usually determined according to the required material throughput. It is also important that the temperature of the return air is within an allowed range.
During normal operation the dry air cools down on its way through the material. This is in part due to the cooling effect of evaporating water. Additionally, the cooling effect of the undried virgin material coming into the drying bin also plays a role.
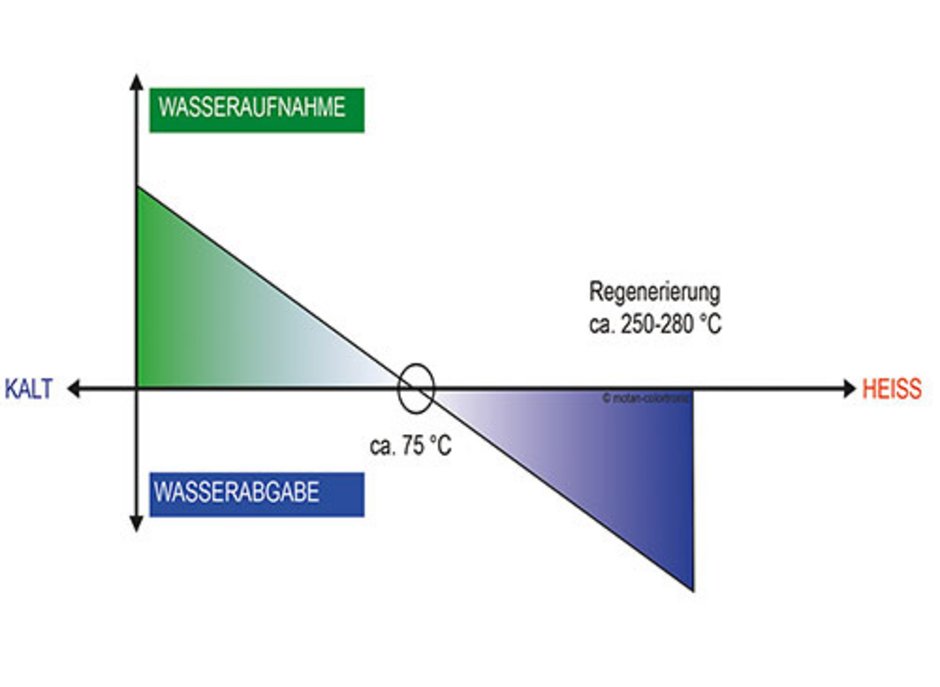
Assuming the material throughput decreases or there is a stop in production, there is a danger that the material can over-dry and possibly be damaged. Because the pre-set dry air amount continues to flow through the material in the drying bin, the temperature of the return air also increases. The reasons for this is that the two cooling effects just described are no longer in effect. In regulated drying systems this can for the most part be prevented with a reduced amount of air.
If increasingly hot air continues to flow through the molecular sieve, the temperature of the desiccant will also increase – resulting in lower water adsorption capacity. At around 70- 80 °C the molecular sieve will no longer adsorb any water. Worst case, the desiccant bed will no longer dry or could even release water. At the same time, it will need to be regenerated more often, using more energy than necessary. To prevent this, the temperature of the return air should remain under 60 °C.
One possibility of cooling the return air to an efficient temperature is the installation of a return air cooler between the exhaust of the drying bin and the desiccant bed. Return air cooler usually operate with water and should be connected to the cooling cycle. At very high temperatures, for example when drying PET, a part of the thermal energy can be regained using an air-air- heat exchanger. Additionally, less energy is then needed for cooling.
Return air temperatures that are too high can also occur when high drying temperatures are needed. For unregulated drying system, temperatures of over 120 °C are already critical. In order to achieve the necessary return air temperature, cooling through evaporated water and cold virgin material is no longer sufficient.
How can a return air cooler be used for your drying process? More information you will find on www.motan.com